Inventory Variant Tracking for Your Online Store: Successful Tips
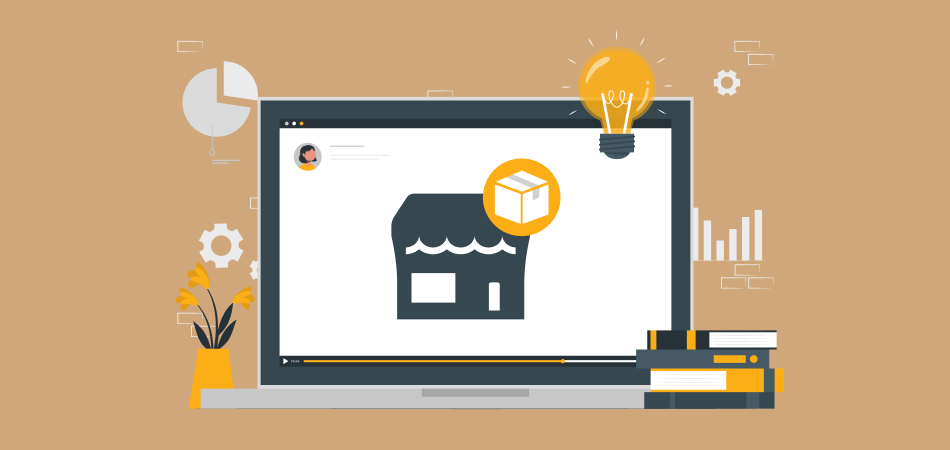
We are in 2024 and the e-commerce business is witnessing competition at its top level, and customer expectations are always increasing. In this situation, effective inventory management has been recognized as a foundation of success. Among various aspects of inventory management, tracking of inventory variants holds an important significance among online retailers.
Read the extensive guide, examining its significance, and difficulties, and offering specific recommendations for its implementation.
Why Inventory Variant Tracking Is Important
Variants are the essence of product diversity in online retailers; they include a variety of features, including size, color, style, and material. From the customer’s perspective, having a variety of options improves the buying experience by meeting their requirements and preferences. The capacity to precisely inventory variant tracking is essential to the success of any e-commerce business.
So why it's so crucial? The average inventory accuracy for the US retail sector is roughly 63%. It is impossible to overestimate the importance of inventory variant tracking. It acts as the foundation that guarantees clients will always have access to a wide range of product selections while keeping ideal stock levels and lowering the possibility of overselling or stockouts. Imagine an online customer searching for a particular type and color of clothing. The merchant runs the danger of upsetting the consumer by advertising unavailable options in the absence of precise inventory variant tracking, which could ruin their shopping experience and cost them the sale.

Furthermore, improving customer satisfaction and loyalty is greatly aided by efficient inventory variant tracking. Online retailers may cultivate trust and confidence in their brand by offering a diverse array of products to clients and guaranteeing their availability in real-time. This approach can lead to repeat purchases and helpful word-of-mouth referrals.
What Does Quality Control Mean
In the case of inventory variant tracking, relies heavily on quality control to guarantee that customers receive the products they want and to reduce the possibility of returns or unfavorable reviews.
Ensuring Consistency
Ensuring consistency in product descriptions and visuals is a key responsibility of quality control in inventory variant tracking. Customers may become confused and frustrated by inconsistencies such as mismatched graphics or disparities in sizing charts. Online retailers can improve the accuracy of variation tracking by regularly auditing product descriptions and photos to find and correct any discrepancies.
Controlling Product Quality
Quality control includes not only maintaining consistency in product data but also confirming the accuracy and consistency of inventory variations. This involves thoroughly inspecting product samples to make sure they adhere to the required standards and requirements. Variants made of different materials, such as cotton and polyester, should be properly labeled and their quality should match that of the client.
Improving Customer Satisfaction
Online businesses can reduce the possibility of returns and exchanges due to inconsistencies or flaws in inventory variants by putting strong quality control systems. This enhances customer satisfaction and loyalty while also assisting in the reduction of operating costs related to processing returns. Consumers are more likely to become repeat customers and brand ambassadors when they receive products that meet or beyond their expectations.
Enhancing Brand Reputation
Furthermore, upholding strict quality control standards in inventory variant tracking is crucial to protecting the reputation of the company and retaining clients. Delivering precise and superior products regularly upholds the brand's reputation for dependability and professionalism and establishes it as a dependable supplier in the eyes of customers. Positive word-of-mouth referrals and higher client retention rates may follow from this.
![]() |
Find Better Supplier For Products DSers Supplier Optimizer - One click to filter out the most proper suppliers for your products |
Continuous Improvement
Online retailers need to be aware of and quick to adapt to shifts in consumer tastes, market trends, and product requirements. Retailers can guarantee that their inventory varieties suit the changing demands and expectations of their target market by asking for and implementing consumer input into their quality control procedures.
What Are the Challenges of Inventory Variant Tracking
As we have learned what does it mean by quality control, let’s discuss what are the challenges in Inventory Variant Tracking.
Overstocking and Understocking
Finding the ideal ratio of overstocking to understocking is one of the most frequent problems in inventory management. Overstocking raises carrying costs and increases the risk of obsolescence for inventory since it ties up valuable capital and storage space. Conversely, understocking leads to lost sales opportunities, disgruntled consumers, and possible loss of the reputation of the company.
Online retailers can use data analytics and demand forecasting tools to predict client demand in order to overcome this difficulty properly. Retailers can avoid the risk of overstocking or understocking by optimizing their inventory levels and taking into account elements like seasonality and promotional activity, as well as by scrutinizing past sales data and market trends.
Seasonal Variations and Trends
Handling seasonal trends and changes presents another challenge in inventory management. Demand for some products may fluctuate throughout the year, with off-peak seasons necessitating modifications to inventory levels and peak seasons driving higher sales volumes. Additionally, having the correct products stocked at the right time requires keeping up with shifting consumer tastes and industry trends.
Online retailers should watch industry trends and carry out in-depth market research to predict seasonal swings in demand to tackle this difficulty. Retailers can limit the danger of excess inventory during off-peak periods and capitalize on opportunities by proactively modifying their product assortment and matching inventory levels to seasonal trends.
Storage and Fulfillment Logistics
For order processing and delivery to go smoothly on time, effective storage and fulfillment logistics are necessary. Ineffective picking and packing procedures, poor inventory storage techniques, and disorganized warehouses can all result in unhappy consumers, higher shipping expenses, and delays in order fulfillment.
![]() |
Place Orders to AliExpress In Seconds DSers Bulk Order - Place 100s of orders to AliExpress in a few seconds with a just few clicks |
Online retailers should invest in order fulfillment technology and warehouse management systems (WMS) to improve inventory storage and expedite warehouse operations to solve this difficulty. Lean inventory management techniques, barcode scanning system implementation, picking route optimization, and warehouse layout optimization can all increase order fulfillment accuracy and efficiency while also improving customer satisfaction.
How to Overcome Hurdles in Inventory Variant Tracking
For e-commerce companies, variant monitoring poses particular difficulties that range from supply chain complexity to SKU confusion. A smooth shopping experience for customers and accurate inventory management depends on successfully overcoming these obstacles.
SKU Confusion and Management
SKU confusion is one of the main issues with variation tracking, particularly when dealing with comparable variants that have distinct stock-keeping unit (SKU) identities. This may result in disparities in inventory, misunderstandings among warehouse workers, and mistakes in order fulfillment. Online retailers should set up explicit SKU management procedures to get around this problem. They should also make sure that every version has a distinct identity that appropriately represents its characteristics.
Using product features like size, color, and style in the naming convention for SKUs can help distinguish between similar versions and expedite inventory variant tracking. Additionally, SKU management may be made simpler and the chance of miscommunication decreased by investing in inventory management software that enables customizable SKU creation and tracking.
Supply Chain Visibility
Effective variation tracking requires maintaining supply chain visibility, especially when working with many suppliers and warehouses. Complicating inventory management and raising the risk of stockouts or overstocking can be caused by limited visibility into supplier inventory levels, lead times, and delivery statuses.
To ensure transparency and visibility throughout the supply chain, online retailers should place a high priority on working together and communicating with their suppliers. The supply chain can be made more visible and coordinated by creating regular channels of communication, exchanging demand and inventory estimations, and putting vendor-managed inventory (VMI) systems into place.
Why Integrate Quality Control and Inventory Variant Tracking
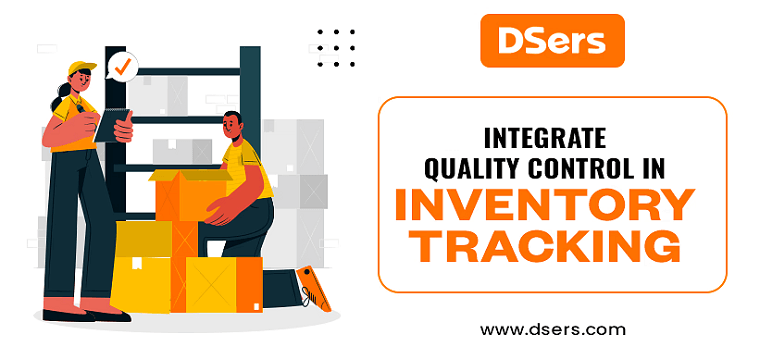
To make sure that the products put up for sale fulfill the requirements and standards and that accurate inventory records are kept, you must integrate quality control and inventory management.
Streamlining the Product Inspection Process
Simplifying the process of inspecting products is one part of combining inventory management and quality control. To guarantee that every variant satisfies the required quality requirements before it is added to the inventory, quality checks must be performed on incoming inventory. Online retailers may decrease errors, lower the risk of stocking subpar or damaged products, and maintain the integrity of their inventory by automating or standardizing these screening processes.
Real-Time Inventory Update
Ensuring that quality control procedures are smoothly connected with inventory management systems to enable real-time inventory updates is another crucial component of integration. As soon as quality checks are finished, inventory records are updated, enabling retailers to precisely monitor stock levels and make well-informed decisions about product availability and replenishment.
Feedback Loop for Continuous Improvement
Moreover, a feedback loop for ongoing improvement can be established by combining inventory management and quality control. Retailers may improve product quality, strengthen supplier relationships, and streamline inventory management methods by using data-driven decision-making to obtain insights from quality control processes, such as recognizing common defects or concerns with specific variants.
End Note
For e-commerce enterprises looking to prosper in the current competitive environment, understanding inventory variant tracking is essential. Online merchants may optimize their operations, improve consumer satisfaction, and foster sustainable growth by placing a high priority on quality control, deploying sophisticated inventory management systems, and proactively addressing difficulties related to inventory variant tracking.
Online merchants may set themselves up for long-term success and expansion in the digital marketplace by embracing the insights and tactics provided in this guide and striving for inventory variant tracking perfection.
Want to find out more? Visit DSers blog today!