Reverse Logistics 101: Definition, Benefits, Types, and So Much More
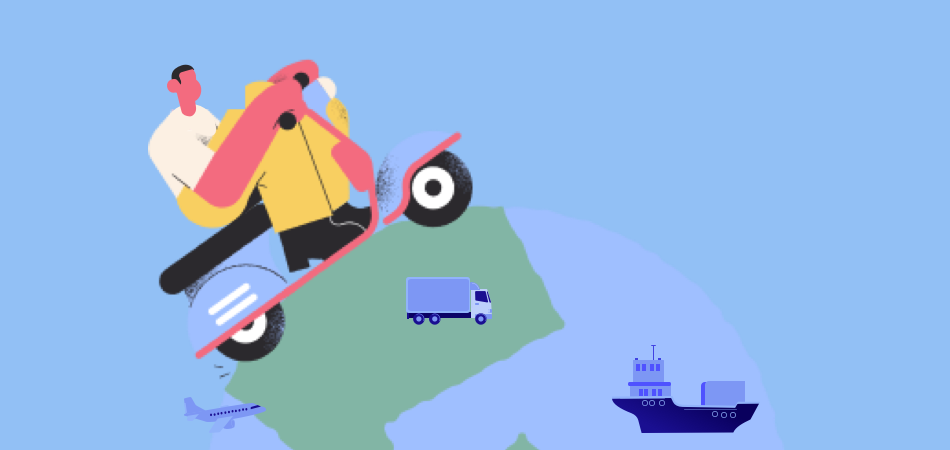
When it comes to supply chain management, the flow of logistics can happen bidirectionally – forward or reverse. You might already be familiar with forward logistics that pushes products toward customers.
Though, reverse logistics can be a new concept as it pulls products from customers. Sound confusing? Don’t worry – simply read this detailed guide to know how the reverse flow in the supply chain works.
What Is Reverse Logistics
Reverse logistics is a common practice in supply chain management that follows a reverse or backward flow regarding the movement of products and services. That is, instead of pushing products from a supplier to a customer, they are pulled from customers instead. Mostly, it helps us complete returns or refunds of products or to recycle/dispose/resale products.

Therefore, it follows stages of planning, controlling, and implementing a cost-effective flow of products and inventory in the supply chain. The flow mostly starts from a customer’s point and finishes at its original supplier or manufacturer.
The number of returns in any eCommerce store can range from 3% to 50% and it can consume a lot of resources. That’s why it is extremely important to optimize this process, particularly for online eCommerce stores.
How Reverse Logistics Works
After covering some basics, let’s dive in a little deeper to understand how the backward flow in logistics works. Ideally, the most important thing you need to consider is the processing of returns. You need to come up with a streamlined channel that will pick up returns from your customers and processes them according to your requirements.
The way you deal with your returns will play a vital role in how you come up with the logistics path. In most cases, the logistics channel has 5 ways of processing things:
Return: This is the simplest step in which products are simply picked from customers. Now, they are either exchanged with a new product or the return of their funds is initiated.
Reselling: In this, the product that we pick from our customers is resold in the market. The reselling of refurbished phones is one of the common examples of this model.
Repair: In case of a faulty product, we first pick the product and then repairs it. At times, the product is repaired at the customer’s end too.
Recycling: This is mostly done with products that are no longer needed by the customer and the supplier. We simply get rid of the product or recycles it into other materials.
Replacement: Lastly, there might be a scenario in which you have to replace a part of the product (like replacing a part of a faulty electronic product) with a new one.
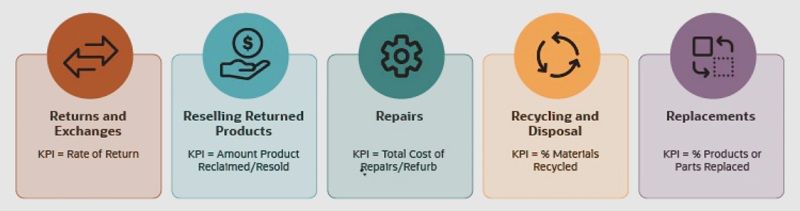
Common Components in Reverse Logistics
As you can see, there can be different ways to fulfill a reverse logistics cycle in supply chain management. Based on the type of products you are dealing with and your process, the overall cycle can have numerous components:
Return Policy
This is the most important component in the backward logistics process that all online store owners should develop in advance. Before you start selling anything, come up with transparent policies for return, exchange, and delivery. You can have a dedicated page on your store to inform your customers about your return and refund policies.
Return Management
Coming up with policies is not enough as you need a streamlined management process to implement them. For this, you need to come up with a viable, controllable, and flexible process. For instance, you need to set up return guidelines, how refunds are processed, timely deliverables, and so on.
Refurbishment
It is a vital process in various eCommerce stores, in which we refurbish an existing product. It is then repaired or rebuilt according to predefined guidelines. Later, we optimize and sell the refurbished product on the store.
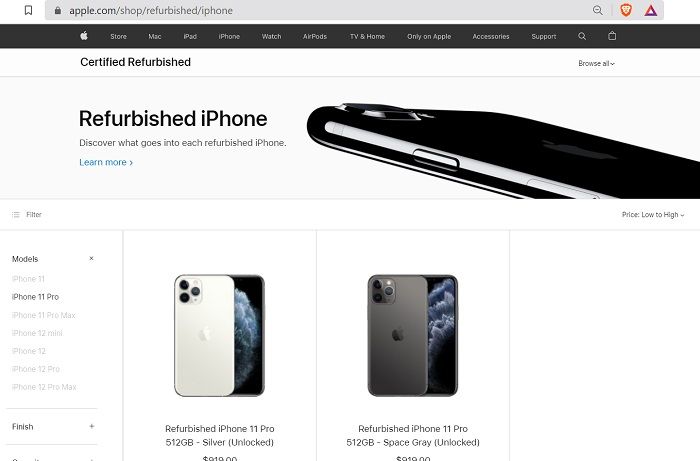
Packaging
Also, you need to manage steps and materials for the packing of products. Several store owners take numerous steps to optimize their packaging materials to save cost and minimize disposals.
Delivery Failure
This is where the forward and backward logistic cycles can intersect. Let’s assume a situation in which your shipping partner couldn’t deliver the product to your customer. Now, you need to come up with a set protocol regarding the reattempt of delivery and what happens when it also fails.
Rentals
Some online stores have also started leasing products. If this is the case with your store, then you must provide a point of pickup for products once their rental duration is over. Also, you need to come up with numerous ways to maintain the quality of products before and after their delivery.
End of Life
Lastly, some products simply reach the end-of-life (EOL) stage after several cycles in the supply chain. For example, if a product is already repaired or refurbished a few times, then you might consider discarding it. Also, numerous unsold goods that you don’t want to keep in your inventory can reach this phase.
Key Reverse Logistics Metrics to Monitor
Reverse logistics can sometimes be a little overwhelming to manage. Thus, if it seems too much, then you must start by focusing on the following key metrics first.
Volume
Needless to say, this simply defines the volume of products you own. You can use a warehouse management system to immediately check the total and an individual number of products that you own. Besides that, you should also identify products with a higher volume of returns.
Condition of Returned Products
At times, suppliers get returned products in the best possible condition while sometimes, they can be damaged. Thus, you should come up with a list of parameters to perform quality checks on returned products. It can help you identify the volume of products that you can readily use or the products that need repairing.
Return of Cost
Furthermore, as you scale up your eCommerce store, you should calculate the overall cost of managing its reverse logistics process. In this way, you can optimize the process and come up with better budgeting too.
Errors
Most importantly, you should have a pre-defined path for the backward logistics process to follow. Based on that, you can easily identify errors in the process and try to optimize them.
Tips to Optimize Reverse Logistics Strategy
Great! By now, you can easily understand the most important components of reverse logistics. Since it can suffer from various financial, operational, and managerial challenges, you must follow some smart tips to get better results. Here are some of the best suggestions offered by experts to optimize your backward logistics strategy.
Tip 1: Try to automate your tasks
It has now become easier than ever to run your supply chain management steps automatically. You can simply install a cloud-based logistics system that will help you automate most of the important work. You simply have to manage everything and can minimize the occurrence of human errors.
Tip 2: Evaluate and change your policies
A lot of online store owners make this mistake, in which they simply stick to their company’s original return policy. You might have come up with those policies in a different frame of mind, and you can end up losing customers because of that. After the pandemic, a lot of online stores have changed their return and refund policies, making them friendly to their customers.
Tip 3: Work with your suppliers
Another smart tip that most online store owners follow is regarding working with their suppliers closely. Consider monitoring the quality of their products and try automating things by installing APIs of your suppliers
Tip 4: Make data-driven decisions
There are numerous tools and platforms that can help you make smarter decisions. You can simply integrate them with your supply chain processes to get valuable data for making smarter choices.
Tip 5: Don’t forget about transportation
Many strategists forget about time and monetary constraints related to the transportation of goods in the overall process. As you come up with expectations related to costing and timing of logistical steps, make sure you consider transportation constraints in mind.
Tip 6: Try to centralize everything
Most importantly, you must have a centralized network connected to every touchpoint of the supply chain process. This will help you monitor everything in one place and save your resources as well.
Explore DSers to Manage Your Dropshipping Store
Since it is tough to handle logistics, you can come up with a dropshipping store instead. For this, you can simply explore DSers, which is the official dropshipping solution by AliExpress.
- On DSers, you can explore a wide range of products from thousands of different suppliers.
- There is also a provision to instantly find the best-rated supplier for any products with its Supplier Optimizer feature.
- You can also manage your stocks, order products in a bulk, come up with bundles, and even map variants.
- DSers is available for free and is fully compatible with leading eCommerce platforms like Shopify, WooCommerce, and Wix.
Conclusion
As you can see, the concept of reverse logistics can get complex, particularly for beginners. Therefore, to make things easier for you, I have listed its benefits, types, and overall process in detail.
I have also included some smart tips that you can follow to optimize the logistics process. Though, to make things even simpler, you can take the assistance of DSers, which is the official AliExpress dropshipping tool.